ANTIKYTERA VISIONLINE ADD
Automated Defect Detection for Industrial Lines
Automated, high-accuracy surface defect detection from microns to millimeters.
VISIONLINE A.D.D. is Antikytera’s precision surface inspection system — built for inline use in demanding industrial environments. It leverages a custom setup and high-resolution cameras and AI to detect and classify surface defects on manufactured parts, ensuring quality without interrupting production.
Automate and Scale
We help businesses automate their processes. This reduces manual tasks, increases efficiency, and allows teams to focus on more strategic activities.
Surface Defect at Micron level
We help businesses automate their processes. This reduces manual tasks, increases efficiency, and allows teams to focus on more strategic activities.
SYSTEM OVERVIEW
Full Setup
- Industrial-grade RGB camera (configurable resolution)
- Optional polarized optics for challenging surfaces
- Controlled lighting system (ring or bar LED)
- Rigid support structure with shock resistance
- Edge computing unit for real-time processing
- AI-powered visual inspection engine
- Defect classification based on training dataset
- Real-time decision system (pass/fail + logs)
- Web-based dashboard or API connection to MES/ERP systems
VISIONLINE ADD SYSTEM
🧠 Continuous Learning AI
The more it sees, the better it gets. At the core of VISIONLINE A.D.D. is an AI-powered engine trained on real defect images — not synthetic simulations.
How it works
Real-Time Visual Feature Mapping
Each part entering the inspection frame is processed via a real-time inference engine using a Convolutional Neural Network (CNN) trained on surface images from your specific domain.
Defect Typing and Confidence Scoring
Once a candidate anomaly is detected, it is passed to a second-stage model (e.g., ResNet-based classifier or MobileNet variant) that maps it to known defect categories:
Incremental Adaptation from Production Feedback
This is where your AI model gets smarter over time. The system includes a modular feedback pipeline.
Benefits of AI-Driven Learning
- Fewer false positives over time
- Better distinction between real / acceptable tolerances
- Adaptability to new product versions or minor changes
- Increased ROI the longer the system runs
Your quality control doesn't just get automated, it gets smarter.
Flexible Use Cases
Built to adapt to your process — not the other way around. The VISIONLINE A.D.D. system is designed as a modular solution that adapts to different inspection needs, depending on your part type, production stage, and defect detection goals.
Gear housing
Detect micro-scratches, pits, casting defects, oxidation spots, or residual machining fluids.
Pineons & Shafts
Inspect cylindrical surfaces for dents, burrs, wear marks, and polishing inconsistencies
Castings & Forgings
Identify surface anomalies such as burn marks, scale, or incomplete material flow
Flexible Integration Options
From raw incoming castings to post-machining final checks, defective parts are flagged and diverted automatically from the main line.
🧪 Pilot Setup & Training
We offer short-term pilot deployments to validate performance on your line.
Our engineers will train the AI using your existing defect archive or capture new samples on-site.
🤝 Proudly Trusted by Industry Leaders

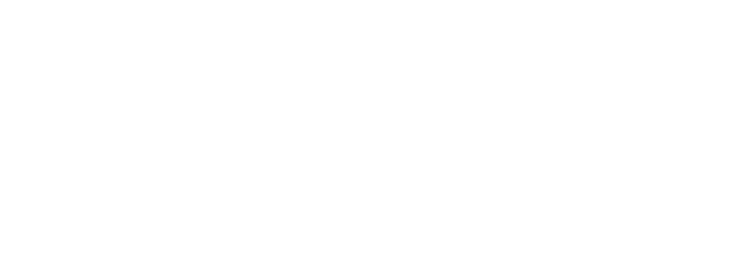


🤝 Let's talk
Whether you're replacing manual inspection or upgrading outdated systems, VISIONLINE A.D.D. gives you a robust, real-time quality control layer built for modern lines.
This website uses cookies. Please read our Privacy Policy here.